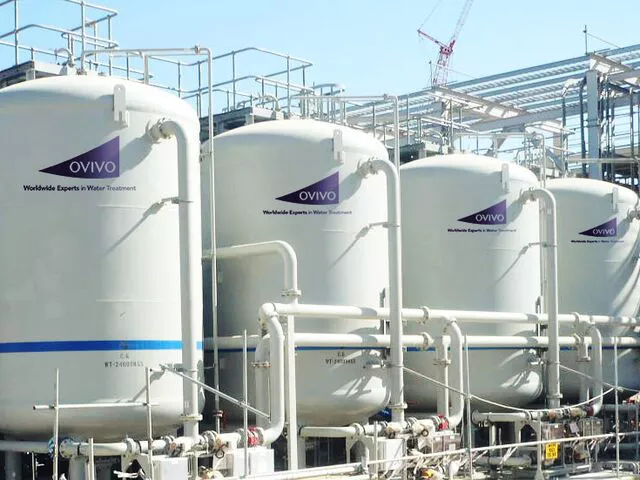
Water Filtration & Purification Technology Solutions
Discover our Technology Solutions
Each Ovivo product is a technologically advanced, complete solution that is refined and adjusted continuously through in-house research and development. A team of Ovivo experts is dedicated to ensuring that all our pre-engineered and custom products meet the highest standards of efficiency, sustainability and reliability.
Explore our industries