MBT
Membrane Thickening (MBT) is a recuperative sludge thickening process in biosolids management that thickens waste activated sludge (WAS) to up to 3 percent solids without polymers, reducing sludge volume along with operating and maintenance costs.
The MBT process uses silicon carbide membranes (SiC) to thicken WAS without the need of polymers or chemicals. It can be retrofitted into any tank configuration in existing wastewater treatment plant.
Contact an ExpertThe MBT process is an environmentally friendly and cost-effective solution in biosolids management. It provides reduced operating and maintenance costs for thickening and significant savings in hauling costs.
Sludge thickening with MBT requires no polymers or chemicals, minimal infrastructure and process footprint, and can be retrofitted into existing tankage. The process thickens WAS on a continuous basis, minimising operator time and ensuring a steady state mode. Sludge is typically two times thicker than that produced by conventional decanting operations in biosolids management which minimises sludge disposal.
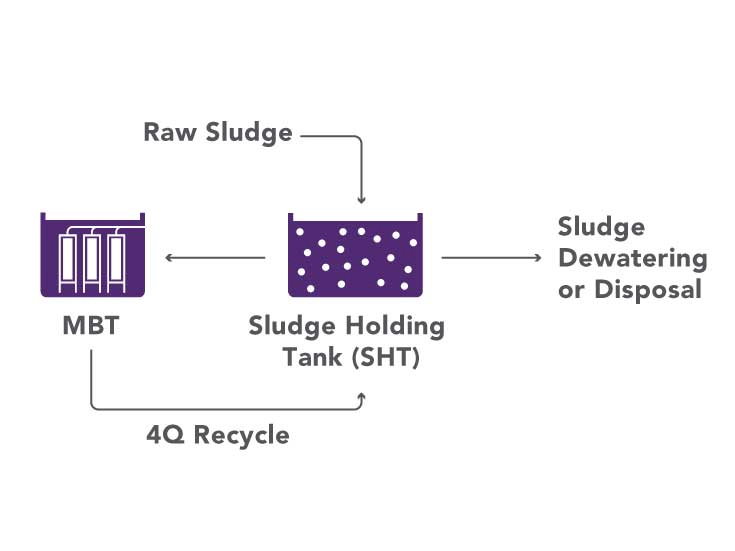
The MBT process consists of a membrane thickener tank and an aerobic sludge holding tank (SHT). All blowers, permeate pumps, recycle pumps, aeration equipment and instrumentation are included in the MBT process package to ensure one source of responsibility.
WAS is fed directly from the liquid treatment process into the SHT. The flow is transferred at a rate of 4Q into the membrane thickener tank via a pump. Sludge is thickened by pulling clean water through the SiC membrane, leaving solids behind. This process is done continuously, which saves time and reduces the need for chemicals or additional materials in biosolids management.
Because of the quality of filtration by the membrane, the permeate from the thickener may be combined with the treated effluent flow that is to be sent to disinfection instead of recycling back to the headworks of the wastewater treatment facility.
The thickened sludge from the MBT is transferred over a weir back into the SHT where it is actively mixed and digested with the help of Ovivo’s TransMAX air diffusers. The end result is WAS that is three times thicker than unthickened WAS and requires less transportation, leading to significant cost savings in biosolids management.