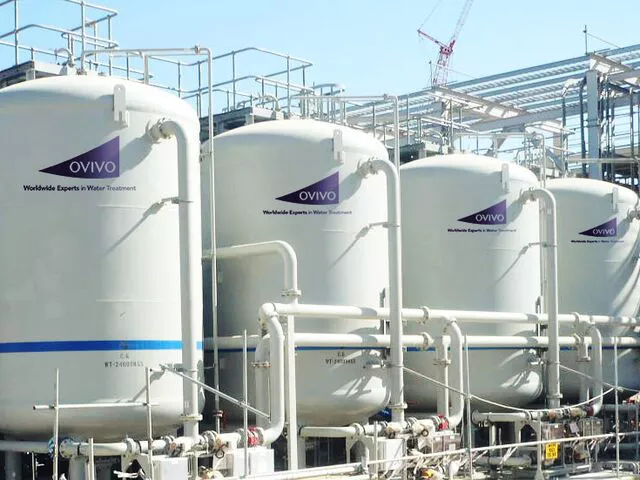
Technologies de purification de l’eau, des eaux usées et des gaz
Découvrir nos solutions technologiques
Chaque produit Ovivo est une solution complète et technologiquement avancée qui est perfectionnée et ajustée en permanence grâce à nos services internes de recherche et développement. L’équipe d’experts Ovivo s’engage à garantir que tous nos produits préconçus et personnalisés répondent aux normes les plus élevées d’efficacité, de durabilité et de fiabilité.
EXPLORER NOS INDUSTRIES